The Nonwovens Institute at North Carolina State University offers a full range of test methods for nonwoven filter media from its Filtration Testing Lab on the Centennial Campus of North Carolina State University. Here we provide a brief primer on filtration test methods followed by a virtual tour of NWI’s state-of-the-art Filtration Testing Lab.
About Filtration Testing
Filtration testing is a critical process used to evaluate the performance of filters in various applications, such as air purification, water treatment, and industrial processes. It helps determine how effectively a filter can remove contaminants or particles from a fluid (liquid or gas) and assesses the filter’s efficiency, capacity and lifespan. Filtration testing is essential in industries like pharmaceuticals, food and beverage, automotive and healthcare, where clean fluids are vital for product safety and equipment longevity. The testing procedures involve assessing parameters such as particle size retention, flow rate, pressure drop and overall filter integrity.
One of the most common methods of filtration testing is particle counting, where a sample of fluid is passed through the filter, and the number of particles is measured before and after filtration. This technique helps determine the filter’s efficiency in capturing particles of various sizes. Laser-based particle counters or optical microscopy are often used to detect particles in fluids. Filtration efficiency is usually expressed as a percentage, indicating how many particles the filter can capture compared to the total number present in the unfiltered sample.
Another key method is the integrity test, often applied to filters used in sterile or critical applications like pharmaceuticals or medical devices. The integrity test ensures that the filter has no defects and is capable of performing its intended task without leakage or bypass of particles. One common integrity test is the bubble-point test, which measures the pressure at which gas starts to flow through the wetted membrane of the filter, indicating the pore size and structural integrity. This method is used to verify that the filter can retain particles of a specific size without damage.
Flow rate and pressure drop tests are also significant in filtration testing, especially in industrial applications. These tests measure how much resistance a filter adds to the fluid flow and how quickly the fluid can pass through the filter under various pressure conditions. A low-pressure drop is ideal because it indicates that the filter is not overly restrictive, ensuring that the system can operate efficiently. Flow rate tests help ensure that filters can handle the required volume of fluid without compromising performance.
Finally, lifecycle testing, or capacity testing, evaluates how long a filter can function before it becomes clogged or needs replacement. This is important in systems where filters need to perform continuously over long periods. During this test, the filter is subjected to a steady stream of contaminants over time, and its ability to maintain filtration efficiency and a consistent flow rate is monitored. Understanding a filter’s capacity allows operators to predict maintenance needs and optimize operational schedules to avoid unexpected downtime or reduced performance.
Filtration Testing Lab Virtual Tour
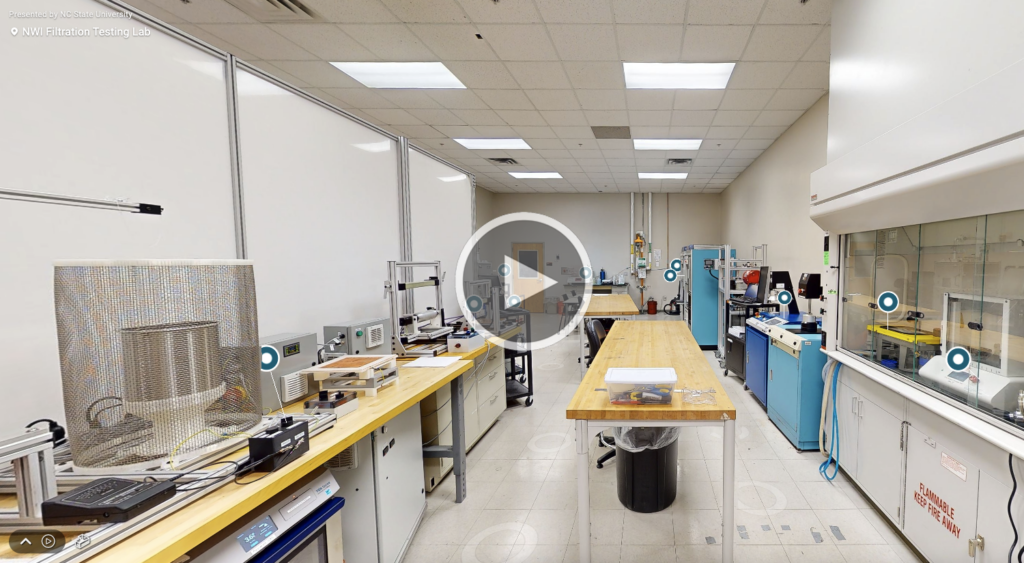
Filtration Testing Lab Capabilities
NWI’s filtration testing capabilities include services for facemasks and respirators, along with filter media for automotive, HEPA and HVAC applications, among others. Importantly, NWI’s Filtration Testing Lab is outfitted with equipment to perform ASTM F2299 testing for the measurement of Particle Filtration Efficiency (PFE) at 0.1 microns.
Testing equipment available in NWI’s Filtration Testing Lab includes:
- PALAS MFP-3000-S fractional aerosol filter test
- Two TSI 8130 machines for filtration efficiency
- Two TSI 3160 machines for filtration efficiency
- Two offline charging and discharging units
- Two environmental chambers for aging and conditioning masks and filter media
- Testing apparatus for the measurement of fluid resistance for surgical masks
- Prototyping facility to produce masks for testing purposes per NIOSH Standard Test Protocol
Why test your filter media at NWI?
- Decades of in-house material testing experience
- ISO 9001 accredited
- ASTM F2299 testing capability
- Strict adherence to good manufacturing practices (GMP)
- Highly competitive pricing model
- Quick turnaround times
To view NWI’s Filtration Testing Lab Virtual Tour, please visit https://bit.ly/4bnnlDQ.
To engage with NWI’s nonwoven filter media and filtration testing experts and/or to book time in NWI’s Filtration Testing Lab, please visit https://bit.ly/43Yt92w.
For more information on NWI’s large pilot- and lab-scale nonwoven production and testing capabilities, please visit https://bit.ly/48IWpx6.
If you would like to learn more about filter media and filtration testing, consider attending the Filter Media Short Course, which will be presented by NWI at FiltXPO™ 2025, Apr. 28-29, in Miami Beach, Florida. For more details, please visit https://bit.ly/3MzcPPp.
* The Filtration Testing Lab Virtual Tour is made possible through a grant provided by NC State’s Digital Education and Learning Technology Applications (DELTA), in support of NWI’s education and training programs. To learn more about DELTA, please visit https://delta.ncsu.edu/.
- Categories: